WELDING MAP

Features
-
The Welding Map module is intended for all projects where there are welding processes. It is designed to work with large welding productions, in the industrial sectors such as gas & oil, petrochemical, electrical, civil, among others.
-
It will provide you with a series of data management options for your projects, which will benefit you in time and costs when evaluating progress, quality, traceability and time.
-
Real-time reports of weld production, progress control, traceability, non-destructive tests, processes, visual inspections, periodical reports, rejects for joints and / or welder, advance control of NDT Piping Class, among many others.
-
Management of PQR (Qualification of Procedures), WPS (Specification of Procedures) & WPQ (Qualifications of Welder) for each project.
-
Control of Booklets and Isometrics automatically.
-
WM Discrimination for workshop and Field
-
Material Management by Lot or Unit.
-
Tell the system what data you want to include in the WM and let SISCORP do the heavy lifting.
-
Among many others
-
MONITORING AND TOTAL TRACEABILITY
-
Administrative
-
Data from location, work (Cost Center) and clients
-
-
Operative
-
NDT Requestt (managers and requesting areas)
-
Weld dates and END order dates
-
-
Construction Management
-
Booklets, Lines and Isometrics, sheets and revision; Stretches and / or KM for Pipelines
-
Isometrics: P&ID, Line Size, Fluid Service, Systems, Lines, Piping Class, Leaves and Rev., Spooles
-
Pipelines: Special crossings, Splices, Valves, among others
-
-
Insert links to important documents and even the isometry drawings directly to the system.
-
Provide the system with the percentages of non-destructive and variable heat treatment tests (before and after). Painting Schemes, Tracing, Application Standards, Systems and Subsystems.
-
Indicate the ranges of welds for each isometric or Section / Km in pipelines and the system will automatically enter them into the welding map containing all the critical information of the isometric and without duplications or shortages.
-
Calculate production equivalent inches in real time.
-
Calculate minor diameter welded in a combination of materials with different measures. Eg: Pipe / Sockolet; Pipe / Tee Reduccion; etc
-
-
Design
-
Discriminate welds of supports and normal welds
-
Discriminate Field welds from Shop welds (FW / SW)
-
PH Id, dates PH, Test Pack, Circuits and Systems & Subsystems
-
Traceability of Materials
-
Traceability Codes by Lot or Unit
-
SAP Traceability Codes
-
Diameters and schedules
-
Material Quality and Descriptions
-
Heat Nro and Certificates
-
Materials with Impact / NACE requirements
-
Providers
-
-
Types of welds
-
Butt, Fillet, etc
-
-
Joint types
-
Welded, Flanged, Electro Fusion, etc
-
-
SPOOLS identification
-
Paq y Tracing
-
Painting schemes and shipments of pieces to paint
-
Isolations
-
-
Production
-
Flexible identification of welds.
-
Shop Weld: Allows you to place letter before and after the meeting number.
-
Ducts: Allows to place pipe numbers of pipes, (before and after welding); Progressive combined with the measurement of the tubes automatically.
-
-
Tell the system if there are welds that should be considered outside the test percentage.
-
Management of Eliminated and / or Cut welds; Finished; Arrested by the client, among other states
-
Welders participating in the weld (singles, pairs or more)
-
Dates of welds and final assemblies, in workshop and field.
-
Visual inspections and WPS used in each weld performed
-
Colors in WM to quickly identify production pending, tests pending, repairs pending.
-
Record release status by dates, of the following processes: Assembly, Welding, Inspection, END, Shot, Paint, Coating, Dispatch, Reception, Assembly; as well as record the documentation generated, in each process.
-
-
Non destructive test
-
Quickly mark and retrieve welds that must be retested for non-satisfaction.
-
Available tests: Thickness Measurement, Magnetic Particles, Ultrasound, Penetrating Liquids, Industrial Scintigraphy, Thermal Treatment.
-
NDT orders with identification sticker, for quick location in the field.
-
Defects and Results Management
-
-
Repair management, Repair stamp, WPS used, date and result.
-
Repair decals for quick identification of the defect location for the repair welder.
-
-
Reports
-
Design and configure your own reports using templates
-
All reports are issued in MS EXCEL format
-
Types of reports
- Welding Map
- Visual inspection
-
Welding Parameters
-
Traceability of Materials (long and short description)
-
NDT, HT orders, Repairs
-
Production control
-
among others
-
Welding Map
-
-
Indicators
-
All indicators are issued in MS EXCEL format
-
Types of Indicators
-
SPOOLES closing status
-
LINE / ISOMETRIC closing status
-
Production and Rejection of Welders (by Welder and / or Piping Class)
-
Distribution of Status NDT Welders
-
Types of rejections committed (by welder, EPS, General, etc.)
-
NDT Production by Piping Class
-
General Rejection Percentage
-
Production Advance (by quantity, inches, date range)
-
State of the Joints
-
among others
-
-
-
Import and export
-
Import daily output from an excel into the system. SISCORP is responsible for verifying that the imported information is consistent and correct
-
Export all pending earrings in MS EXCEL format. (Production and / or NDT)
-

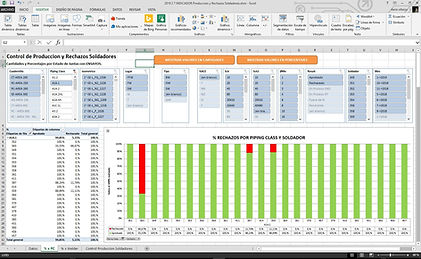
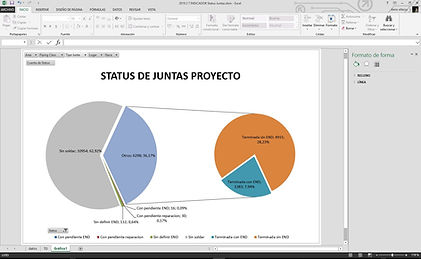

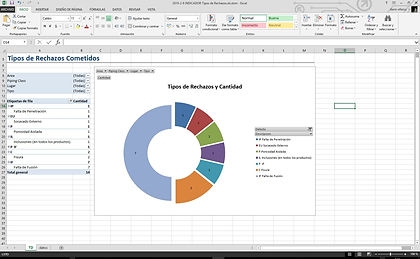
STICKERS
Welding Map is the only system of this type that allows you to issue STICKERS for monitoring and executing Non Destructive Testing, SPOOLS Identification and Traceability Identification works.
When issuing NDT Order Reports, Traceability and Materials, or Repairs, you can choose to issue the STICKERS with the corresponding information to be attached to the side of the weld. Help and facilitate field tasks in marking and tracking materials using this practical identification system.
(Requires special A4 paper with adhesive)

